The Ultimate Guide to: Construction Handover Packs
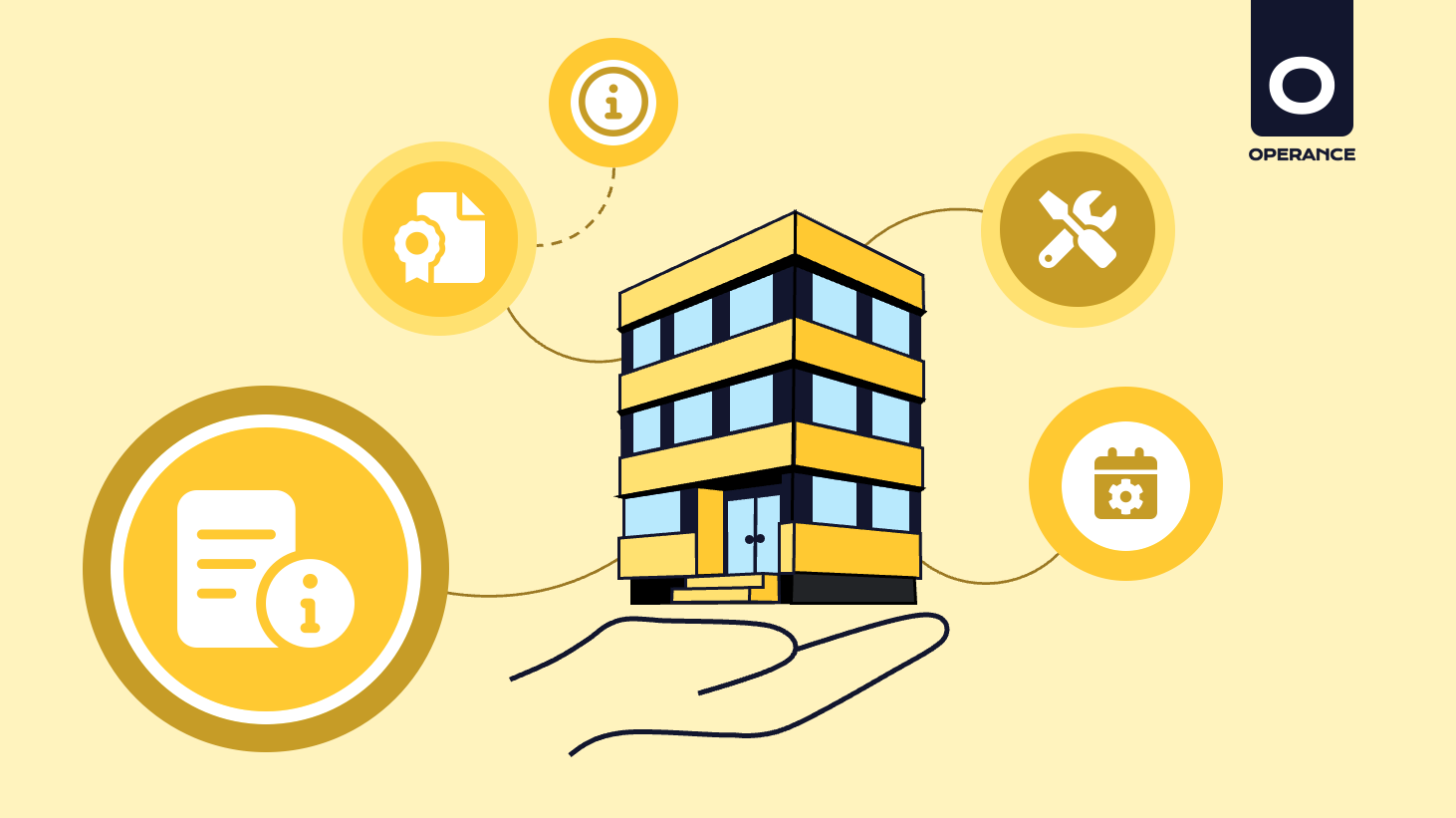
Intro
Whether you are about to provide the keys to a new multi-million-pound school, a refurbished hospital ward, or a new 2-bed home; owners, operators and occupiers expect a handover pack, commonly known as the ‘as-built’ information, or mistakenly referred to as the ‘O&M manuals’ – more on this later!
Asking a contractor or modular builder what they include in theirs is a bit like asking what their ideal Christmas dinner looks includes. Generally speaking, they’re more or less very similar, but there’s always a bit of variation in there, not to mention the level of quality in regard to ingredients and execution.
So what should contractors include in their handover pack? Well, that’s the first trap many fall into; it’s not their handover pack!
For instance, when designing new features for Operance, we don’t simply dream up new features that we think users will love; we ask the users what features they would love. I say this not just as a metaphor, but our user is the same as yours. In fact, we call our imaginary user ‘Jeff’.
Jeff could be the new school’s Caretaker, the residential block’s Building Safety Manager, the factory’s Asset Manager, or, the hospital’s Facilities Manager. In summary, Jeff is the person that needs the handover pack in order to operate, maintain and keep the new facility safe and efficient at all times.
It is, therefore, Jeff’s handover pack, not the contractors. But not just Jeff; others will benefit from the information too, such as Jeff’s boss, his colleagues, his building occupants (e.g. commercial tenants), the building owners, visitors, subcontractors and many, many more.
But hey, we probably don’t need to tell you this; you’ve probably been given the exact requirements from the client, right? They have no doubt stated that they expect to receive an O&M Manual, maybe a Health and Safety File too, or perhaps, just one or the other. They may have also asked for a Building User Guide and a Building Logbook. If they are a digitally-minded client, they will no doubt have asked for a finalised BIM model and, if you’re lucky, a side of COBie to go with it!
A common problem we see here with the client listing out these requirements is quite simply ‘copy and paste’. It’s probably not even the client asking for the information; it’s more often than not their project manager lifting text from Employers Requirements (ERs) elsewhere and dropping it in to save some time, without any consideration of what the actual client wants or, indeed, what Jeff needs.
The handover pack, its contents and its structure are often very subjective, with the person requesting it often not knowing the difference between an O&M and a H&S file, a Building User Guide and a Building Logbook.
So, to help, we decided to pull together a list (along with a brief description) of each section you may find in a quality Construction Handover Pack, starting with an understanding between Traditional, Digital and Smart O&Ms and the Construction Handover Pack, then we delve into the contents that could include the following;
Traditional v Digital v Smart ‘O&Ms’
Operations and Maintenance (O&M)
Health and Safety (H&S)
As-Built Design Information
Building User Guide (BUG)
Building Logbook (BLB)
Traditional v Digital v Smart ‘O&Ms’
Types and Forms
Let’s begin with a brief deciphering of the various types and forms of ‘O&Ms’;
- Traditional: Paper-based information, provided in ring binders, stored on shelves.
- Digital: PDF-based information, provided on CD’s and USBs, stored in ‘waterfall-type’ filing systems.
- Smart: Data-based information, provided, stored and updated in an ‘agile’ web and mobile application.
O&Ms v Construction Handover Packs
Now, let’s tackle one of the most misunderstood concepts in construction, the elephant in the room; the use of the term ‘O&M’.
The ‘O&M manual’ is often used to describe the entire and complete ‘Construction Handover Pack’, when in fact, the O&M is a separate section in itself, merely forming part of the greater collection.
“The whole is greater than the sum of its parts” – Aristotle
I’m going to casually throw some theory at you now to explain; bear with me, it should make sense!
‘Systems Theory’ is the interdisciplinary study of ‘systems’, which are formed by cohesive groups of interrelated, interdependent components that, when all put together, form parts of the complex whole, i.e. in this example, the Construction Handover Pack.
Every system (the sections of the Construction Handover Pack, i.e. Health and Safety) has causal boundaries and is influenced by its context, defined by its structure, function and role, and expressed through its relations with other systems (i.e. Operations and Maintenance). A system is, therefore “more than the sum of its parts”. Changing one component of a system (i.e. a Risk Register within H&S), may affect other components or the whole system.
A system is, therefore, any set of distinct parts that interact to form a complex ‘whole’, in this instance; the Construction Handover Pack.
Closed v Open Systems
A ‘closed system’ is not affected by its environment, but an ‘open system’ is, meaning what happens outside of the system has an effect on the system itself.
This is the major difference between ‘Traditional’ and ‘Digital’ O&Ms (i.e. paper-filled ring binders and pdf-filled filling systems) and a ’Smart O&M’ (digital, dynamic, open and full lifecycle data systems).
A Smart O&M, or more precisely, a Smart Construction Handover Pack, is an open system which enables continuous inputs (the information you continuously enter), throughputs (the practice of continuously operating and maintaining the facility) and outputs (the standard of the facilities environment and experience as a result of the standard of the operations and maintenance, as a result of the standard of information input) throughout the building’s lifecycle – all whilst keeping an audit trail of everything (i.e. the golden thread).
A smart Construction Handover Pack must enable a ‘feedback loop’ to be open and truly ‘smart’.
A feedback loop provides continuous information back to the system by connecting the outputs to its inputs, i.e. learning from the standard of the facility as a result of the information and operations and maintenance.
For instance, a feedback loop could predict changes in patterns of behaviour, which is why really advanced clients are starting to investigate smart buildings, digital twins and the Internet of Things (IoT) to predict maintenance requirements proactively rather than reactively, in real-time.
- A ‘negative feedback loop’ indicates a problem that needs to be resolved, for example, a boiler that has broken down and needs repairing due to poor misuse and a lack of servicing.
- A ‘positive feedback loop’ identifies outputs that have worked well, for example, low energy costs as a result of careful energy consumption use and monitoring.
Thus, a feedback loop is a means of confirming if the building is a success or a failure; if it is the latter, it should signal the corrections that need to be made.
Systems Management
But all this means very little without the role of management. The owners of the building are responsible for defining the inputs at the very beginning. They should manage the following:
- Inputs: consider the operator’s and occupier’s needs in terms of the O&M inputs (the information) they need to create a safe, harmonious building experience for all.
- Throughputs: monitor the throughputs (the practice of operations and maintenance) and use the inputs to create the desired outputs.
- Outputs: manage the outputs (the building standards and experiences) into the environment.
- Feedback: monitor for positive and negative feedback loops and make changes necessary to alleviate any negative ones.
Traditional paper/pdf ‘O&Ms’ are incapable of receiving feedback loops; they are ‘closed systems’.
They rely on one input, a stagnant record of a set date in time (i.e. handover), with little or no way of adding new inputs via feedback loops during its lifecycle. They have no way of reflecting what is actually happening during the occupation phase.
Then there’s the general functionality of the inputs (i.e. the information). Ask yourself, whatever Construction Handover Pack ‘system’ you hand over to clients now, how easy is it to search, share, edit, update, supplement with new information, and use the information to operate and maintain buildings?
If your answer is that you probably can’t do any of those things with your current way of defining, curating, accessing and maintaining your Construction Handover Pack, then you might be surprised at how easy it is to switch to a smarter solution, such as Operance.
Why not give our Chief Sales Officer, Ian Hetherington a call on 07775 597214, or drop him an email at ian.hetherington@operance.app to discuss? He might even throw in a 20% discount for your first proof of concept project should you mention the code POC20!
Operations and Maintenance (O&M) Manual
Ok, now we better understand O&M’s as a component, i.e. one of the many cogs in the bigger system, the Construction Handover Pack; let’s now delve into the contents of Operations and Maintenance (O&M) ‘Manual’. The O&M Manual is a collection of all the information relating to its origin, form, operations and maintenance of the key components (i.e. boiler) that make up the systems (i.e. heating system) and the cohesive grouping (i.e. the building).
Components
Examples of ‘components’ generally found within a building and that could be detailed in the O&M Manual:
- Boiler
- Light Fixture
- Air Handling Unit
- Plasterboard
- Shower Unit
- CCTV camera
- Fire Alarm
- Elevator Controls
Systems
Examples of ‘systems’ generally found within a building and that could be detailed in the O&M Manual:
- Cold and Hot Water Systems
- Emergency Lighting Systems
- Heating, Ventilation and Air Conditioning System
- Internal Wall System
- Plumbing Systems
- Security System
- Fire Protection System
- Elevator System
Component and Systems Information
Examples of specific O&M information contents;
- Manufacturer’s Details: key information that identifies the company and key contact information should users have questions or concerns. This could include the company name, contact information such as the company’s address, phone number, email address, website, product support, country of origin, compliance information and perhaps even social media links.
- Data Sheet: a comprehensive data set regarding a product’s traits and characteristics. This could include the product’s technical specifications, design, size, dimensions, materials, power requirements, safety warnings, performance, and functionality.
- Drawings: specialist products, whether they be bespoke (i.e. a passenger lift) or ‘off-the shelf’ (i.e. a disabled platform lift), should be accompanied by their relevant designs, which could include elements of architecture, structural, mechanical and electrical engineering. These will provide dimensions of the product and give insight into the areas of the product you cannot see with the human eye, such as what’s behind the wall, for instance.
- Operating Manual: this should provide instructions on how to use a product safely and effectively. The specific content of an operating manual can vary depending on the product, but in general, it should include safety information, setup and installation instructions, operating instructions, maintenance and care guidance, service guidance (plus any pre-agreed service plans) and troubleshooting.
- Warranties and Guarantees: legal information informing the owner of their rights and obligations in the event of component failure and/or dispute. The main difference between a guarantee and a warranty is that a guarantee is usually free, whereas a warranty typically includes a premium for the cover (much like a form of insurance). The great thing about a guarantee is that it is legally binding and adds to your rights under consumer law. Each one is different, but they tend to be useful if:
- If something’s gone wrong after the handover and you want a repair or replacement (you may/may not) have to prove you didn’t cause the problem.
- You bought an item abroad, and the manufacturer is based in the UK.
- A trader’s gone out of business, and there’s a problem with the goods or service they provided.
The paperwork should state the following:
- How long does the warranty or guarantee last.
- What you’re entitled to, e.g., a refund, repair or replacement.
- If you can’t find the guarantee or warranty, contact the seller or trader and ask if they have a copy of the manufacturer’s contact details.
- Commissioning and Testing Results and Certificates: i.e. a record of how the facility and its systems and components have been tested to meet relevant standards. It provides evidence that the asset is able to deliver on its purpose. It could include:
- Air Permeability Test
- Acoustic Test
- Mechanical and Electrical System Tests (e.g. ventilation, emergency lighting, solar photovoltaics (PV), plumbing installations, air source heat pumps, heat recovery units)
- Water Legionella Testing
- Simplified Building Energy Model (SBEM)
- Energy Performance Certificate (EPC)
- Brochure: your clients and end users may also find a copy of the manufacturer’s literature quite useful too. This could provide less technical information than others may prefer. It could provide detailed 3D imagery and examples of the product in use. It should provide an overview of all the other information as listed above, just in a more succinct manner. Because of this, a brochure is not a substitute for the technical data required in order to properly operate and maintain the product.
Take, for instance, a boiler. The O&M should provide the technical specifications, the manufacturer’s details, its expected performance, a test certificate, a warranty and all the detail required in order to efficiently and safely operate and maintain it. It should also provide information about the collective heating and/or hot water system that it is connected to. If you need detailed information on the boiler (and its own components), such as how to service it (and when), you need to search the O&M manual for the boiler and its collective information.
Building Information
But it’s not just information about the individual components/assets and the collective systems that the O&M holds; it should also provide the following information regarding the facility itself, such as;
- Project Description: this should provide a detailed overview of the original project. It should outline the facility’s purpose, scope and key features. It could also describe the objectives of the project (i.e. what the facility is designed to achieve and how it will benefit stakeholders). It must include the location of the project and the teams involved. It may also provide details of the project’s timeline and budget.
- Type of Construction: description of the materials used, building techniques applied, description of the structural design and architectural style, the age of the building, if not new, and if any previous works have been carried out back to its original construction (if known).
- Key Contacts: contact information for key personnel; this should include contact details for the building owner or property manager, as well as the principal contractor, principal designers and any key personnel responsible for the building’s design, build, supply and/or fix of major assets and maintenance and operation procedures.
- Defects Procedure: it’s very rare, sadly, that a project will handover with zero defects. Most projects are delivered with a number of ‘patent’ defects (those which are patently obvious, such as a cracked pane of glass), and ‘latent’ defects (those in which manifest themselves later, such as subsidence). In either case, there should be an agreed defects procedure in place in which end-users can follow to accurately report and provide a definition of what’s wrong. The contractor should be able to receive, acknowledge, investigate, prioritise, resolve, communicate and document the response.
- Asset Register: a schedule of the components that form part of a building. An asset register may be prepared for every component in a building or just for the ‘active’ assets that require regular inspection, maintenance, cleaning or replacement, such as building services components.
- Completion Certificates: a document that confirms that the building has been constructed in accordance with the approved plans, specifications, and relevant building codes and regulations. It is usually issued by the local building control authority or a qualified inspector after they have conducted a final inspection of the completed building. It indicates that the building is safe and meets all the regulatory requirements. Mortgage lenders or insurance companies may require it before they will provide financing or coverage for the building. Additionally, it may be required as evidence of compliance with building regulations when the building is sold or leased. The completion certificate is also a legal requirement for Higher-Risk Buildings (those that are at least 18m tall, or 7 storeys high and have at least 2 residential units, or is a hospital or care home) and must be presented when applying for a Building Assurance Certificate from the new Buiding Safety Regulator.
- Planned, Preventative Maintenance (PPM): A proactive maintenance schedule in which work is scheduled to occur regularly and consequently documented once it has occurred. The PPM schedule is performed to help preserve a property’s condition, prevent problems from occurring, and avoid failures or breakages. Ultimately, a properly implemented and managed PPM schedule will protect the underlying value of the building and reduce unnecessary expenses and reactive maintenance costs. It will also protect the owner/owner’s organisation by ensuring they stay on top of statutory requirements like gas safety certificates or LOLER inspections. Regular tasks could include:
- Boiler Servicing
- Condition Surveys
- Roof Inspections
- Lift Engineering Insurance Inspection
In summary, an O&M is a bit like the owner’s manual you get with a car, except for a building or structure. It is often referred to more generically as the building owner’s manual – but this again can be often confused, in this instance, with both the Building User Guide and the Building Logbook. Whereas the Health and Safety (H&S) file is required by law under the Construction (Design & Management) Regulations, the O&M manual is usually an Employer’s Requirement that forms part of the building contract. The O&M contains information on the operation and maintenance of the building.
Health and Safety (H&S) File
A Health and Safety ‘File’ is a collection of all information and documents relating to the facility’s health and safety handed over to the building’s owners, operators and occupants.
Like all other documentation in the Construction Handover Pack, it is compiled during the construction phase by the Principal Designer (PD) and handed over to the building owner or manager upon completion of the project. The project’s Principal Contractor (PC) must provide the PD with information for inclusion. Should the PD’s appointment be completed prior to handover, the file must be passed on to the PC, who must then ensure it is reviewed, updated and revised to take into account any changes that may have taken place between the date of the principal designer’s completion and the completion of the work.
However, unlike the other documentation in the Construction Handover Pack, the Health and Safety file is a legal requirement in the UK, as set out in the Construction (Design and Management) Regulations 2015. These regulations state that the building owner or their representative must ensure that a building Health and Safety file is prepared and kept up-to-date for all projects involving construction work, including any construction work involving more than one contractor. This includes most building projects, including new build projects, refurbishment work, and extensions.
The point of the H&S file is to provide the building owners and operators (or the Accountable and Principal Accountable Persons) with a level of detail proportionate to the risks of the project in respect of how to operate and maintain the building or site safely and how to deal with potential hazards or emergencies. Note that this is not a guide on operating and maintaining the building specifically or in detail, as this information is provided in great detail in the O&M, and summarised in the Building User Guide; the H&S file should simply explain how to do it safely.
If you need to know if something is safe to do or where a hazardous material is, you would look in the H&S file. Unlike the O&M manual, the Health and Safety file just contains information specific to health and safety. What’s safe, and what hazards building owners, operators, and occupants should be aware of? The Construction (Design and Management) Regulations 2015 (Regulation 12) states;
“The principal designer must prepare a health and safety file appropriate to the characteristics of the project which must contain information relating to the project which is likely to be needed during any subsequent project to ensure the health and safety of any person.”
The H&S file, therefore, contains health and safety information for the future use and maintenance of the building. It should provide relevant information to inform the ongoing safety of the building or site, and the planning of future project works. It does not need to include information about the construction works carried out during the relevant project unless it may affect future works. The H&S file should be kept up to date as changes are made to the building or its use.
Here is an overview of the general sections and contents you could expect to find within the Health and Safety File;
Surveys
There are various types of pre and post-construction surveys that could be carried out and should therefore be included for information as it may inform either the ongoing operations and maintenance of the facility or the further development of it. Some of the most common types of surveys are:
-
Building Condition Survey: assessment of the overall condition of a building, identify any defects, and provide recommendations for repair and maintenance.
-
Dilapidation Survey: carried out before and after a construction project to record the condition of adjacent properties and identify any damage that may have been caused during construction.
-
Structural Survey: assessment of the structural integrity of a building and identify any defects or weaknesses that may affect its stability or safety.
-
Measured Building Survey: carried out to produce accurate measurements and drawings of a (usually existing) building, including floor plans, elevations, and sections.
-
Asbestos Survey: identification of the presence and location of asbestos-containing materials (ACMs) in a building and provide recommendations for safe removal and disposal.
-
Archaeological Survey: identification, assessment, and record of archaeological sites and artefacts in a particular area. They are usually conducted by trained professionals, such as archaeologists or cultural resource management experts, who use a variety of methods to locate and document archaeological sites. They typically involve a combination of fieldwork, research, and analysis. The results are used to understand the historical and cultural significance of an area, to develop plans for site preservation or excavation, and to comply with cultural resource management regulations.
-
Topographical Survey: This survey is carried out to produce a detailed map of the land and its features, including contours, boundaries, and utilities.
-
UXO Bomb Survey: identification and locating of unexploded ordnance (UXO), which are explosive devices used in past conflicts but did not detonate. UXO can include bombs, grenades, artillery shells, and other types of explosives that pose a risk to public safety.
-
Utilities Survey: also known as a Buried Services survey or Underground Utility Detection survey, this is conducted to locate and map out the underground utility services that are buried beneath a particular area. These services may include things like gas lines, water pipes, electrical cables, fibre optic cables, telecommunications lines, and other buried infrastructure to identify the exact location of these underground utilities to prevent accidental damage during construction, excavation or drilling works.
-
Drainage Survey: a detailed assessment of the drainage system in a property or an area. It is conducted to determine the drainage system’s condition, functionality, and efficiency and to identify any issues or potential problems. It is typically recommended that a Drainage Survey be conducted regularly, especially for older properties or those with a history of drainage problems. Clients usually require it at handover to prove the drainage system has been completed without any hidden defects.
-
Environmental Surveys: assessment of the potential impact of a project on the natural environment. Some of the most common types could include:
- Ecological Survey: This survey is carried out to assess the impact of a construction project on local wildlife and ecosystems and to identify measures to mitigate any negative impacts. It may involve surveying the area’s plant and animal species and evaluating their habitats and breeding patterns.
- Arboricultural Survey: carried out to assess the health and condition of trees on a site and identify any trees at risk of damage or removal during construction. It may also involve identifying measures to protect trees that are to be retained during the construction process.
- Bat Survey: carried out to assess the presence and activity of bats on a site and to identify any risks to their habitat or breeding patterns posed by the construction project. It may involve surveys of bat roosts, feeding grounds, and flight paths and identifying measures to protect bats during construction.
- Bird Survey: carried out to assess the presence and activity of bird species on a site and to identify any risks to their habitats or breeding patterns posed by the construction project. It may involve surveys of nesting sites, feeding grounds, and flight paths and identifying measures to protect birds during construction.
Statutory Approvals
These refer to the legal requirements that must be met before a building can be constructed, altered, demolished or occupied. The specific types of approvals and conditions will vary depending on the location and type of building. However, here are some of the most common examples:
- Planning Approval and Conditions: In undertaking particular types of development (e.g. new build or refurbishment), Local Authorities will need to ensure that any necessary Statutory Approval is obtained and that it complies with any legal waivers, consents and conditions attached to the granting of the approval. It is important to have evidence of the permission and conditions agreed upon to build and utilise the facility legally.
- Building Regulations Approval: This separate approval ensures that the proposed building meets the minimum safety, health, and energy-efficiency standards set out by the government.
- Environmental Impact Assessment: only applicable for projects that could significantly impact the environment. It is used to assess the potential environmental impact of the proposed building and to identify any measures that can be taken to mitigate those impacts.
- Listed Building Consent: only applicable if the proposed building is a historic or listed building. This approval is required to ensure that any alterations or repairs do not compromise the historical integrity of the building.
- Fire Safety Approval: required for buildings that are deemed to pose a significant fire risk, such as high-rise buildings, hospitals, or schools. It ensures that the building has adequate fire safety measures in place.
- Health and Safety Approval: only applicable to buildings that are deemed to pose a risk to the health and safety of the occupants. It ensures that the building complies with all relevant health and safety regulations, such as those related to ventilation, lighting, and hygiene.
- Drainage and Sewage Approval: required to ensure that the building has adequate drainage and sewage systems in place.
- Access and Mobility Approval: This approval is required to ensure that the building is accessible to people with disabilities and meets all relevant accessibility standards.
- Public Right of Way Approvals: necessary for any construction, alteration, or repair work that affects public roads and pathways. The approvals ensure that the work is done safely and does not cause unnecessary disruptions to traffic or pedestrians. Here are some of the common types of roadwork approvals:
-
- Planning Permission: Any roadwork that involves building or changing the layout of a road will require planning permission. This ensures that the proposed changes comply with the local zoning laws and environmental regulations.
- Road Closure Permits: If the roadwork requires the closure of any part of the road, a road closure permit will be necessary. This allows the road to be closed for a specified period and ensures that the closure does not cause undue disruptions to traffic.
- Traffic Management Plans: for any roadworks that could affect the flow of traffic. It should outline the measures that will be taken to ensure the safety of pedestrians and motorists and minimise traffic disruptions.
- Road Excavation Permits: required if the roadwork requires excavation of the road. It aims to ensure that the excavation is done safely and does not cause damage to any underground utilities.
- Street Works Notices: For any roadwork that takes place on a public road, a street works notice must be issued to the local authority. This notice outlines the work’s scope and the project’s duration.
- Utilities Notifications: if the roadwork requires the interruption of any utilities such as water, gas, or electricity, the relevant utility companies must be notified in advance. This ensures that the utilities can be safely disconnected and reconnected without causing disruptions to service.
- Noise and Vibration Management Plans: required if the roadworks are likely to generate significant noise or vibrations. It outlines the measures that will be taken to minimise any disturbances to nearby residents.
Risks Assessments & Method Statements
A risk assessment aims to identify potential hazards and assess the likelihood and potential consequences of those hazards in order to develop strategies to mitigate or manage the risks. It’s the process of identifying, analysing, and evaluating potential risks or hazards associated with a particular activity, process, or situation. For example:
- Residual Risks: identification of residual risks (risks that remain whereby the design team were unable to eliminate them from the design of the project), general hazards and the measures put in place to control them. Residual risks could be relevant to ground conditions, asbestos, fragile materials and other hazards.
- Fire Risk Assessment: a fire risk assessment is an evaluation of the risk of fire occurring in a building or facility and the potential harm that may result from a fire. The assessment is conducted to identify potential fire hazards, evaluate the likelihood of a fire occurring, and assess the effectiveness of current fire safety measures. A fire risk assessment should typically involve a physical inspection of the building, including its structure, layout, and any equipment or materials that could increase the risk of fire. The assessment may also take into account the activities carried out in the building, the number of people present, and any special considerations, such as the presence of vulnerable individuals or hazardous materials.
- Method Statements: descriptions of the specific steps to be taken when carrying out operational and maintenance tasks. Information could include safe working loads and structural information. An example of a task could be the use of a ‘cherry picker’ in an internal foyer to change light bulbs at height, for example. They should be developed in consultation with competent persons and be reviewed and updated as necessary.
- Hazardous Materials: information on materials used during construction and any potential hazards associated with them.
- Hazardous Substances: details of any hazardous substances used or stored on-site and the procedures for dealing with them.
Policies, Procedures, Records and Inspections
-
Health and Safety Policies: detailing any overarching principles and values with regards to health and safety, i.e. responsibilities of workers, supervisors, and managers; hazard identification and assessment; incident reporting and investigation; visitors policies, and training requirements.
-
Permit-to-Work Systems: used to control high-risk activities, this is a formal document that authorises specific work to be carried out and ensures that all necessary precautions have been taken to mitigate any associated risks.
-
Training Records: a record of all training provided to end-users at the time of handover and for any training given during the occupation phase. It could also include site induction, job-specific, and refresher training. These records should include details such as the date and duration of the training, the name of the trainer, and the topics covered.
-
Safety Inspections: a record of all required inspections, certifications, and tests performed on the building’s safety-related systems and equipment, including fire safety inspections, electrical safety inspections, and elevator safety inspections. There should also be details of the suggested regular safety inspections that should be carried out during occupation to identify any hazards or areas for improvement. The findings of these inspections should be documented, and any necessary corrective action should be taken.
-
Safety Systems Testing Schedule: the regular maintenance and testing of safety equipment and systems such as fire alarms, emergency lighting, and ventilation systems should be scheduled out.
-
Emergency Procedures: including evacuation plans and contact details for the emergency services and key stakeholders in the event of major emergencies, plus contact details for local non-emergency services and key stakeholders to call for assistance in the event of minor emergencies.
As-Built Design Information
An evidential record of how the building has been designed and ‘as-built’ at the time of handover. As-built drawings can be provided by the project’s design team (e.g. architect, civil and structural engineer, mechanical and electrical engineers, specialist consultants, specialist contractors and suppliers).
As-built design information goes beyond just drawings which are traditionally provided in PDF format, but it is now not unusual for clients to also request copies of the designers ‘as-built’ 3D models also (see BIM at the bottom of this list). It must contain the information required before drawings are created too. You should, therefore, provide the following;
Design Preparation
- Strategies: such as Design and Access Statement, Dismantling Strategy, Fire Safety Strategy, MEP Strategy, Roof Access Strategy and Rainwater Harvesting Strategy.
- Specifications: such as architectural, civil, structural, mechanical, plumbing and electrical specifications.
- Calculations: including foul water, surface water, foundations and structural calculations.
Designs
All elements of design should be recorded and provided, complete in the final ‘as-built’ version, such as;
- Architectural: such as general arrangements (GAs), elevations, sections, fire safety equipment positions, fire escape plans, and site plans.
- Structural: such as foundation plans and sections, structural frame elevations, sections and plans.
- Civils: such as grading plans, drainage plans, details and sections, water supply plans and road and pavement plans, sections and details.
- Mechanical: such as hot and cold water supplies, piping and instrumentation plans, schematics and isometrics.
- Electrical: such as electrical supply distribution plans, wiring diagrams, schematics and lighting layouts.
- Landscaping: such as planting layouts, hardscape plans and irrigation plans.
- Specialist Designs: such as Acoustician and Multi-Use Games Area (MUGA) plans.
- Subcontractor Designs: such as platform lifts and secondary steel staircases.
BIM
BIM is a process supported by various tools, technologies and contracts involving generating and managing digital representations of facilities’ physical and functional characteristics and components.
At practical completion, the final fully audited and approved Building Information Modelling (BIM) information. BIM information should be handed over to the client or facility management team; this could include the following:
- AIM Model: the final ‘as-built’ recorded federated model (i.e. all design models combined into one combined, overlayed model) representing the asset configuration at handover is called the Asset Information Model (AIM). The AIM should be ‘systemised’ using the completed system breakdown structure, which forms part of the agreed data model. The best practice is to use the OpenBIM IFC Schema, which includes the COBie data model. A suitable class library (i.e. Uniclass 2015) should be successfully implemented as defined in the client’s Exchange Information Requirements (EIR) to define the asset types. The class library should be compiled within the IFC data schema. If requested within the EIR, the model should include all relevant data related to the building’s design, construction, and operation. This may include information such as geometry, material specifications, and equipment locations. Whether federated or not, the model(s) should be fully checked with any final coordination and clash issues removed. It should also be checked that the information fully aligns with the client’s EIR and the various BIM Execution Plans (BEP).
- COBie Data: Construction Operations Building Information Exchange (COBie) data is a standardised format for exchanging information about a building’s assets. This data should be included in the BIM handover and may include details such as equipment specifications, warranty information, serial numbers, warranty information, and maintenance records.
If you are a contractor or modular builder and need help delivering your client’s BIM requirements, then you might be surprised how many of your industry colleagues our Operance Digital Services team already work with. Why not give our Head of Digital Services, Dave Peacock a call on 07429 869804, or drop him an email at dave.peacock@operance.app to discuss further?
Building User Guide (BUG)
A Building User Guide is a document that provides information about how to use and maintain a building, its systems, and its equipment. The guide is intended for the building’s occupants and is designed to help them understand how the building works and how to get the most out of it. It is a summary of the Operations and Maintenance (O&M) Manual, designed to give none technical users an overview of how to operate and maintain the facility.
The BUG typically includes information on the building’s layout, including floor plans and room functions, as well as details on the building’s heating, ventilation, and air conditioning (HVAC) systems, lighting, plumbing, and other systems. It may also provide guidance on how to operate and maintain specific equipment, such as elevators, fire alarms, and security systems.
In addition to providing information on the building’s physical systems, the user guide may also include information on policies and procedures related to building use, such as rules for parking, waste disposal, and common area maintenance.
A well-designed BUG can be a valuable resource for building occupants, helping them to feel more comfortable and in control of their environment and reducing the need for support and assistance from building management or maintenance staff. It should focus on information relating to the management of people and how they interact with the building. It should also provide a level of detail appropriate for the individuals that occupy or otherwise use a property.
In summary, the BUG provides the end users/occupants of the building with a simple, quick and easy guide to the everyday functions of the building in order to ensure a safe and healthy work environment while complimenting the efficient operation of the building to the full potential provided by the design.
For a more detailed overview of the building User Guide (BUG), please find our previous article: The Ultimate Guide to Building User Guides.
A building user guide should provide essential information such as the following:
-
Introduction: A brief overview of the purpose and scope of the building user guide and the intended audience.
-
Building layout and features: This should include floor plans, room functions, and descriptions of key building features such as entrances, exits, elevators, and stairs.
-
Building systems: This should provide information on the building’s heating, ventilation, and air conditioning (HVAC) systems, lighting, plumbing, electrical, and other systems. It should include instructions on how to operate and maintain these systems, as well as any safety precautions.
-
Building policies and procedures: A clear and concise description of the building’s policies and procedures, including hours of operation, access, parking, security protocols, waste disposal, water management and common area maintenance.
-
Emergency procedures: Detailed information about emergency procedures, including evacuation plans, emergency contacts, and emergency response protocols.
-
Maintenance and repairs: Information about the maintenance and repair of the building’s facilities and systems, including procedures for reporting problems, expected response times, and more.
-
Energy efficiency and sustainability: Information about the building’s energy-efficient and sustainable features, including tips for reducing energy consumption and minimising waste.
-
Health and safety: Whilst more detailed information can be found in the Health and Safety File, and the Health and Safety Summary, the BUG could provide basic information about health and safety in the building, including tips for promoting a safe and healthy work environment.
-
Emergency procedures: This should include information on emergency procedures such as fire safety, evacuation plans, and first aid procedures.
-
Contacts: This should include a list of key contacts such as building management, maintenance staff, security personnel, emergency services, and the keyholders register.
-
FAQs: Frequently asked questions related to the building and its operation can also be included in the user guide.
-
Appendices: Additional resources, such as contact information for building management and maintenance staff, maps, and emergency response plans.
Building Logbook (BLB)
A Building Logbook (BLB) is a document that also contains a record of the building’s design, construction, operation, and maintenance history. However, much like the Building User Guide (BUG) is a high-level summary of the information found within the O&M Manual for general operations and maintenance of the building, the Building Logbook (BLB) is a summary of the O&M information relevant to energy and sustainability.
The BLB is an essential tool for building owners, operators, and maintenance staff to help ensure that the building operates efficiently and safely throughout its lifecycle. It is intended to be a live document in which to record ongoing ‘as-performing’ building maintenance and energy performance information in use during the occupation phase.
The BLB enables end-users, most notably the operators, with a place in which to record how the facility performs in use.
The BLB satisfies the Part L 2006 of the Building Regulations requirement to provide records of ongoing building energy performance for new buildings and in existing buildings when the services are changed. It is also a key requirement in order to meet certain sustainability standards such as BREEAM.
The building logbook should contain information on the following:
- Introduction: This section provides an overview of the building, its purpose, and the intended audience for the logbook. It also includes information on the purpose of the logbook and how it is organised.
- Design and Construction: This should include drawings, specifications, and details of the building’s construction, materials, and systems.
- Commissioning: This should include information on the commissioning process, including commissioning plans, test procedures, and results.
- Operation: This should include details on the building’s operation, including schedules for system operation, maintenance, cleaning and any changes made to the building’s operation over time.
- Maintenance: This should include a record of all maintenance activities, including repairs, replacements, and upgrades, as well as any maintenance schedules, checklists, inspection records and component failure records.
- Energy Usage: This should include records of the building’s energy usage, such as electricity, gas, and water consumption, as well as any energy-saving measures implemented. It should also include any records of environmental assessments or sustainability measures.
- Health and Safety: This should include information on any health and safety measures taken, such as risk assessments, safety procedures, and accident records. It could also include a record of any training on safety procedures for building occupants.
- System Upgrades and Replacements: This should include details of any upgrades or replacements of building systems, such as HVAC, lighting, and fire safety systems. It could also include records of any system testing or commissioning activities that were carried out as part of these upgrades or replacements.
- Contacts: This section includes a list of key contacts such as building management, maintenance staff, security personnel, and emergency services.
The building logbook should be kept up-to-date and accessible to all relevant personnel, including building management, maintenance staff, and contractors.
Outro
So, in summary, a complete Construction Handover Pack should provide all the information and documentation necessary for the safe and efficient operation of the building and for informing any further development, modifications or renovations that may be required.
It’s important to realise that the old adage of garbage in, garbage out is incredibly pertinent when it comes to defining and providing handover information. The lower the quality of the information provided, the lower the efficiencies, safety standards and general value of the end asset.
There should be many competent persons involved in the provision of handover information; designers, contractors, consultants, technical authors, manufacturers, suppliers, subcontractors and more. The contents of the documents should never be left to just one person. No one person on the planet is competent, qualified or experienced enough to know everything about everything in regard to your building. It is, therefore, a team effort.
But let’s not forget, even with all the competent persons involved and providing all the information you asked for, ask yourself, “Is it what Jeff needs!?”.
Get end users involved at the start! Seek input from the persons who actually need this information; it shouldn’t just be a box-ticking exercise. In fact, let them have access to the information as it is being developed, giving them a real chance to understand the facility well before handover and not just during the Government Soft Landing (GSL) period.
We hope this guide has been informative and useful. Should you believe we have missed something or want to provide general feedback, please feel free to contact the author and our Chief Product Officer and co-founder Scott Pilgrim at scott@operance.app.
Want to know more? Contact us to arrange a demo today: https://www.operance.app/request-a-demo/
NEWSLETTER
Revolution Is Coming
Subscribe to our newsletter so we can tell you all about it.
You can unsubscribe at any time and we don’t spam you.
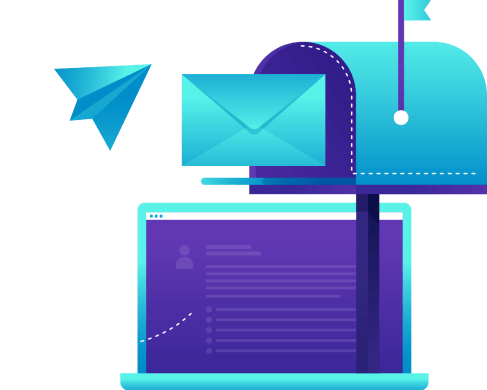